Improve reliability — prevent operational disruptions
Step 4 of the BIOGASmax process
If a biogas plant is to be profitable in reality as well as on paper, it needs to be stable and run with few disruptions. Malfunctions and interruptions in operation keep the plant personnel from their planned routine tasks and cost money. Malfunctions and long periods of servicing also mean erratic plant operation, which often results in reduced biogas yields. However, malfunctions can often be avoided or at least significantly reduced, meaning that investments often pay for themselves in just a short time, thanks to process optimization.
Remove or shred foreign and disruptive matter in the biogas plant as early as possible
Foreign and disruptive matter inevitably gets into biogas plants together with liquid manure, renewable materials, and organic waste. In the form of stones, metal, or pieces of wood, they cause blockages in pumps and gate valves, and clog pipes. They can, however, be easily avoided or significantly reduced by checking deliveries and storing silage on fixed silo surfaces. In many cases, however, that is not enough, and it is necessary to work out how disruptive matter can be removed. A RotaCut with a foreign matter separator separates out foreign and disruptive matter or reduces it to an unproblematic size. This helps to reliably avoid disruptions and prevents wear in the plant components downstream. A cutter can be installed or retrofitted at many points in the plant.
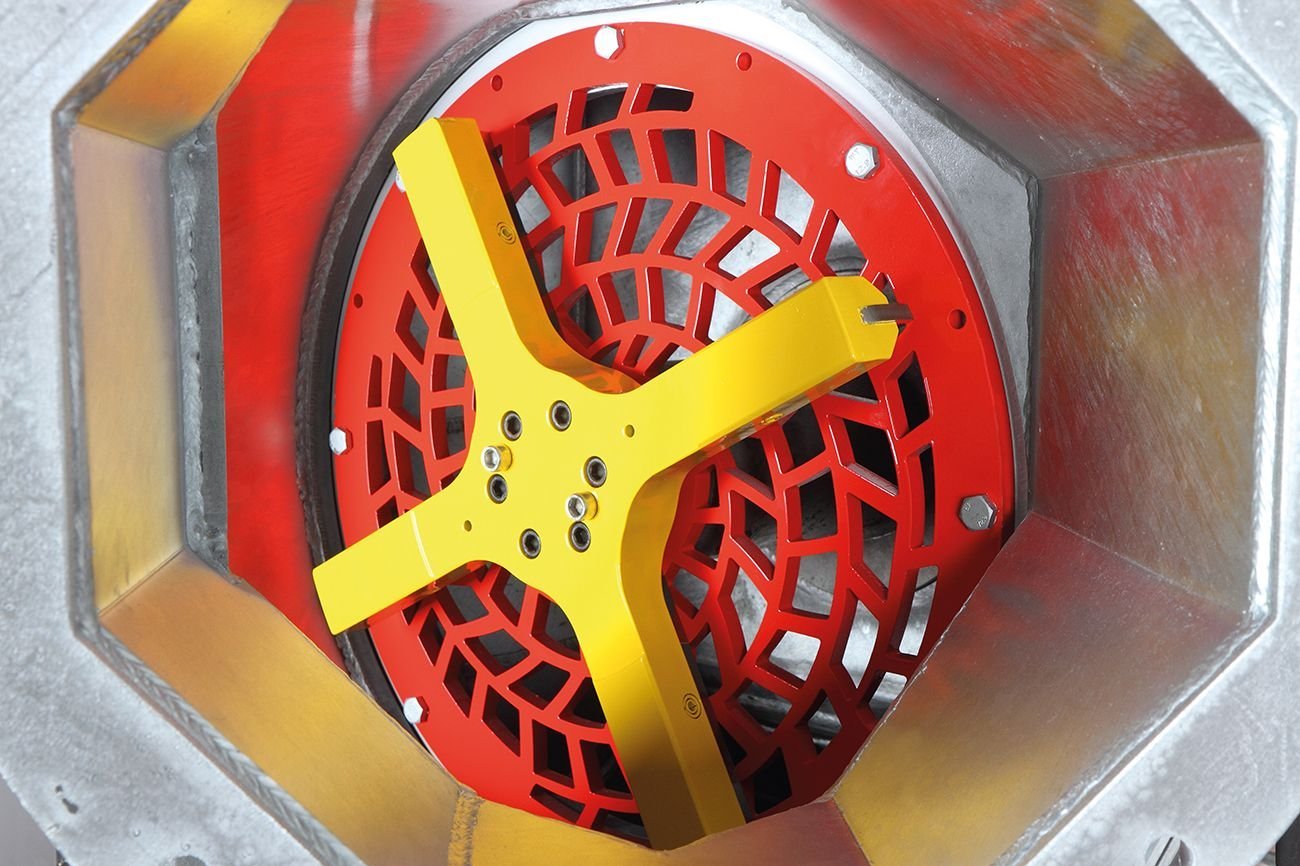
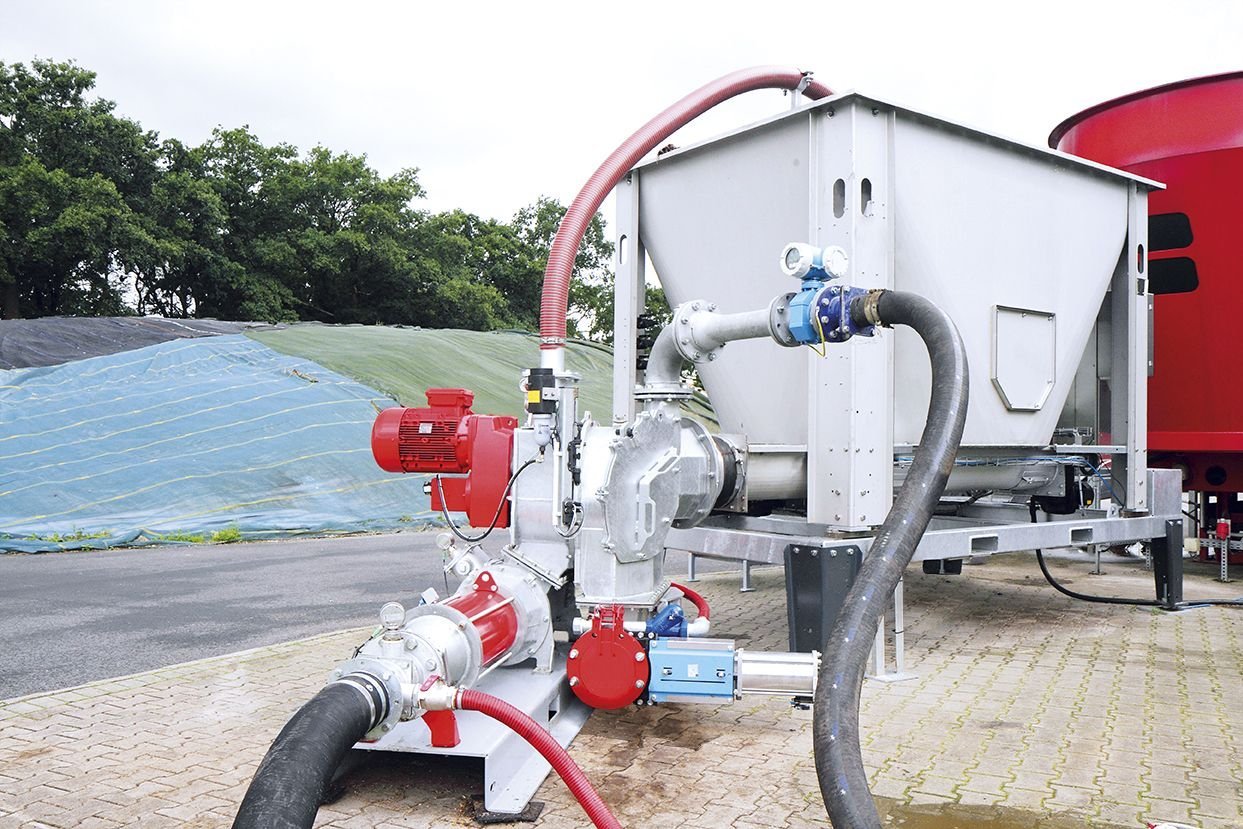
Prevent fiber buildup and clogging in your biogas plant
Fibrous matter is a necessary part of operations in biogas plants. A large number of fibers therefore enter the plant in substrates such as dung and grass silage. Straw twine, nets, etc. can sometimes not be avoided either. Simple modifications can eliminate fiber traps in the pipes and fittings, preventing clogging. Using a cutter actively prevents fiber buildup and clogging in overflows or heat exchangers: It cuts up the fibrous matter and treats the organic suspension effectively. This prevents unplanned disruptions that would require immediate intervention.
Ensure thorough mixing in the digesters and prevent surface crust
In addition to clogging and buildup, fibers also cause solid layers of surface crust. The viscosity of the substrate in the digester rises, and the digester content is not mixed properly. Using a cutter homogenizes and disintegrates the suspension. In addition, the viscosity of the organic suspension and the tendency for crusting are significantly reduced. The contents of the digester are mixed reliably and error messages from overloaded mixers—up to and including complete failure—are avoided. This increases operational reliability considerably.
Feed alternative biomass reliably with advanced solid matter feeders
Alternative biomass, such as dung, whole plant silage, sugar beets and potatoes, is becoming ever more prominent. It is often cheaper and makes crop rotation more flexible. However, such substrates often bring a lot of foreign matter and long-fibered material into the biogas plant, when the plant's solid matter feed is often designed for corn silage. Long fibers and foreign matter lead to malfunctions and failures. In such cases, it is worthwhile to switch to a flexible solid matter feeding system that includes a RotaCut, such as the PreMix, or to retrofit a RotaCut. Before the entry point into the digester, this system will separate out heavy material, shred foreign matter, and homogenize the organic suspension, thus preventing disruptions.
Prevent gas becoming trapped in biogas plant components and pipes
It is not always 100% possible to prevent gas from becoming trapped, but a carefully designed pipe layout can significantly reduce it. Or it can accumulate the gas at a high point deliberately designed for this purpose and release it from time to time.
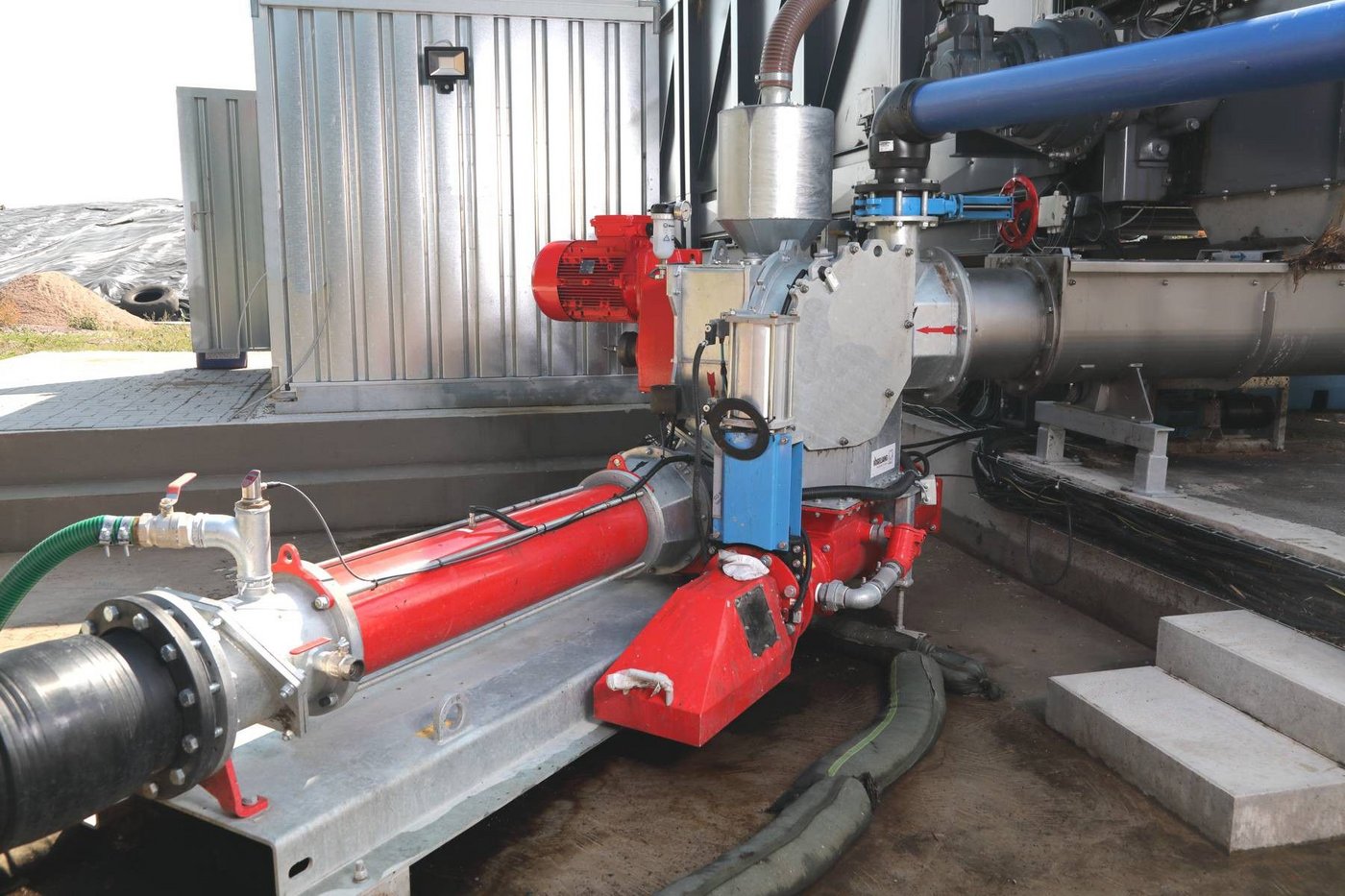
Reliable lifting from deep pits
Pumps in biogas plants often have to lift the material they pump, while evacuating gas or air from empty pipes. That means they have to dry-lift substances like liquid manure from deep pits. With optimized connections, e.g. in the form of connector boxes, the suction capacity and dry-run capability of a rotary lobe pump is significantly increased. This eliminates malfunctions and service interventions caused by the pump running hot, no longer lifting, or pumping unevenly.
Start your analysis now
We would be happy to show you what systematic process optimization can do for you!
Are you interested in an analysis of your plant, want to find out more about BIOGASmax, or have a question? Complete the form below and your consultant will contact you as quickly as possible. Or use our online form to send us the most important specifications of your biogas plant. We work with you to analyze your biogas plant and identify potential for process optimization.
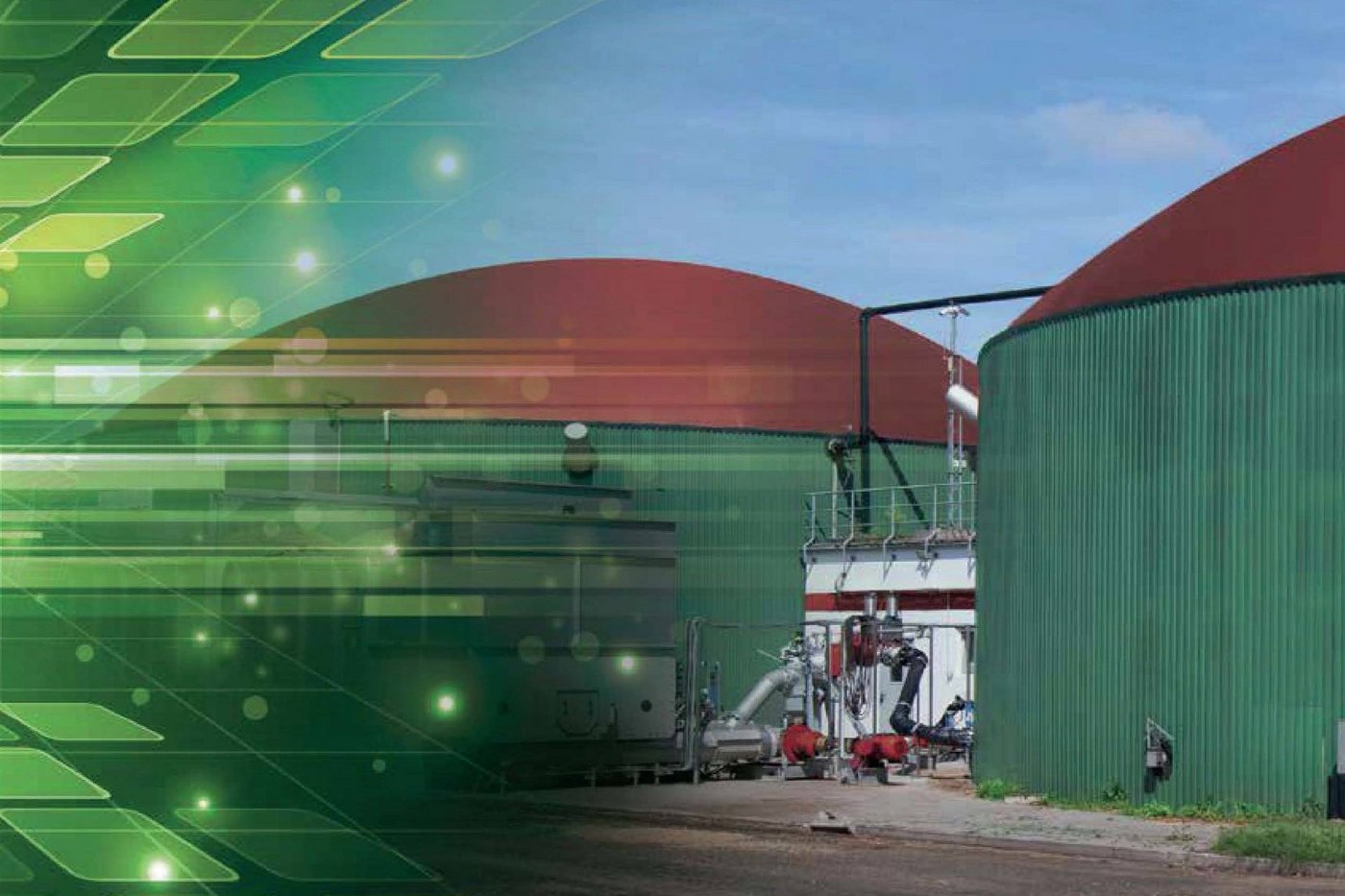
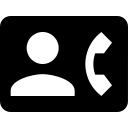
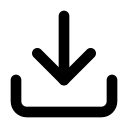
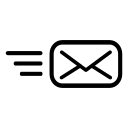