Rotary lobe pumps for tank filling and emptying
Industrial applications in the tank filling and emptying industry
Market requirements
Pump technology which is fast and dosing accurate
Vogelsang solution
Rotary lobe pumps of the VX series and IQ series
The filling, draining and cleaning of stationary tanks and tank vehicles requires high throughput, as well as toughness and precision. The fact that Vogelsang rotary lobe pumps are also resistant to dry running is especially useful for complete pumping of a tank's contents. If this were not done, solid matter would collect at the bottom of the tank, gradually restricting its storage capacity. Due to the arrangement and thread of the lobes in industrial pumps from Vogelsang, the liquid is pumped evenly and without pulsation, independently of its viscosity. The design also ensures a high suction force. Using the innovative InjectionSystem, foreign matter (e.g. in waste oil) is also pumped collision-free, without damaging the lobes.
Vogelsang industrial pumps are equally suitable for the pumping of heating oil, vegetable oil, diesel or biodiesel in industrial ports or oil depots, as well as for pumping processes in tanker trucks or ships. The pumping direction of the highly efficient pumps is reversible, the compact design, especially of the IQ series, saves space and enables quick, cost-efficient on-site maintenance without the need for dismantling. A wide range of different lobes also allows the use of Vogelsang products for pumping substances such as heavy fuel oil, kerosene, petroleum or methanol in refineries. Even in membrane bioreactor technology for the reuse of process water in refineries, rotary lobe pumps are installed because the option to reverse the flow direction facilitates control of the backflow and pumping processes.
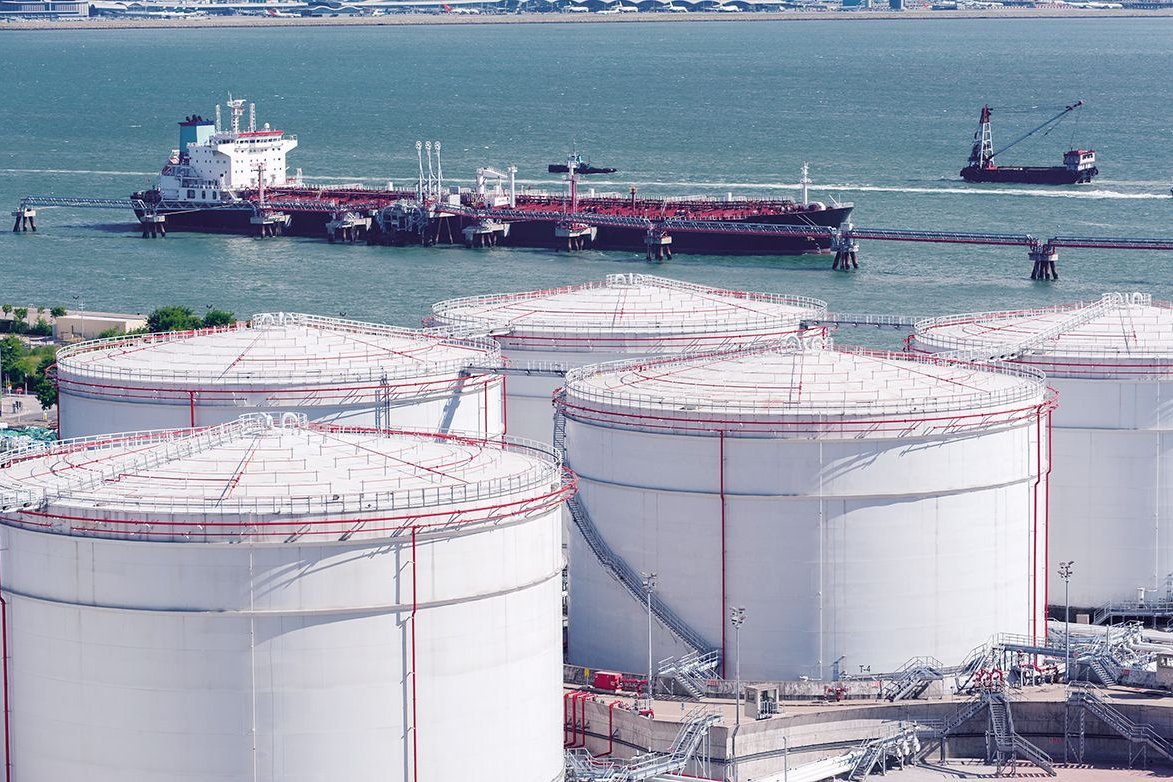
Media processed during tank filling and emptying
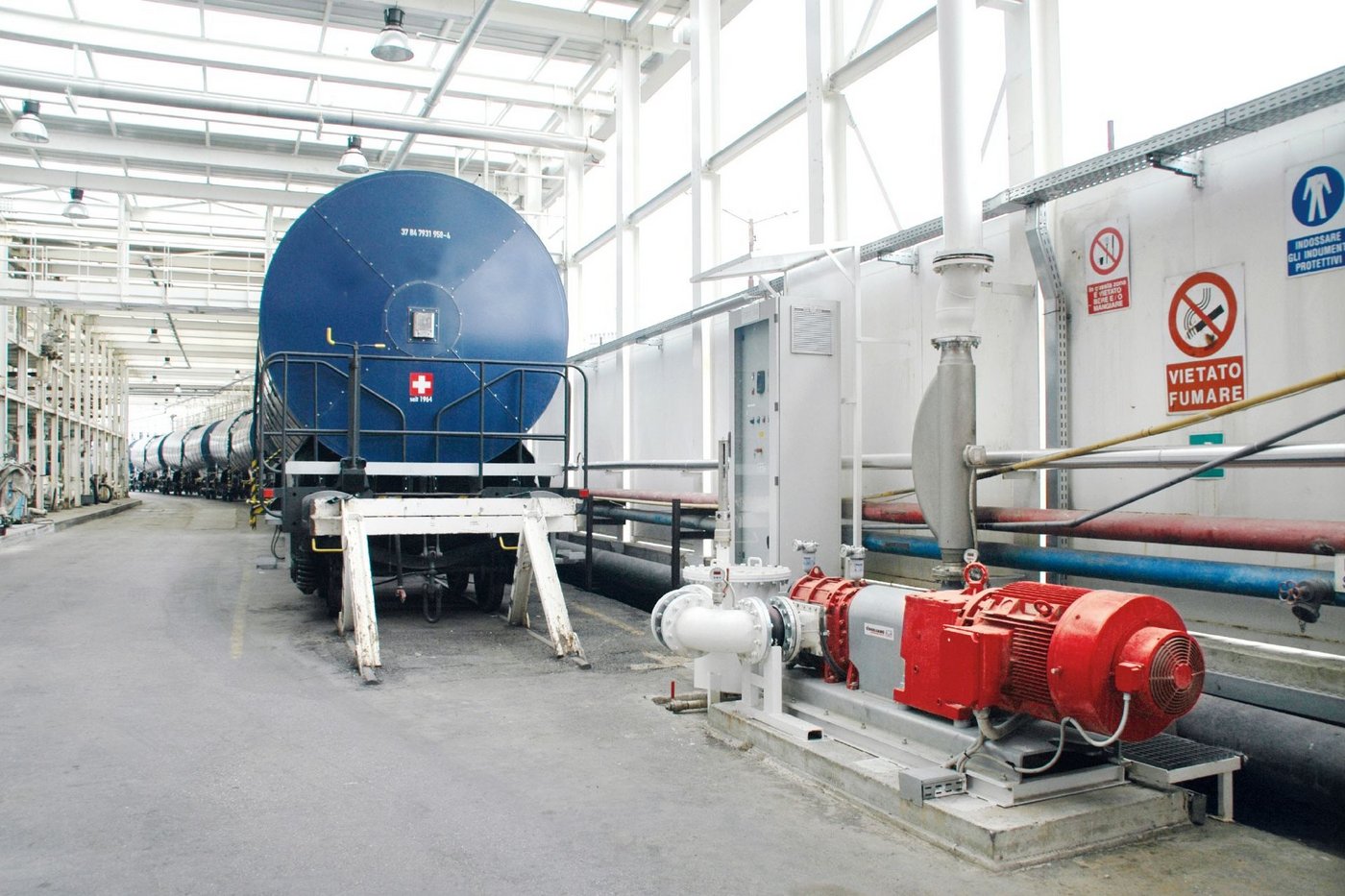
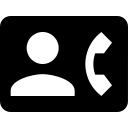
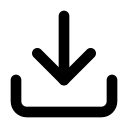
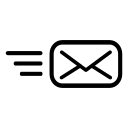