Pumps for the ceramic industry
Industrial applications while producing ceramic
Market requirements
Pumping of viscous and abrasive media at a low pressure
Vogelsang solution
Rotary lobe pumps of the VX series and IQ series
In the ceramic industry, even pumping of typically highly viscous and abrasive media is of great importance. This is because the homogeneity of sludge and glazes determines the quality of the final product. These kinds of slow-flowing media also require a high pumping power, necessitating high speeds and leading to strong shaking and jarring movements, depending on the pump design.
Rotary lobe pumps are pulsation free and more energy-efficient and quieter than air-driven diaphragm pumps commonly used in this industry. Due to their compact design, the Vogelsang models in particular are extremely low-maintenance and easy to service. The product-specific arrangement of the lobes in the housing creates much greater suction force despite low torque, and also allows reversal of the flow direction. This rotary lobe technology is also resistant to dry running and extremely resistant to solid matter and impurities that can occur both in the sludge necessary for production and also in washing and waste water. This is not only good for the product but also makes sense economically to use Vogelsang industrial pumps in ceramic production.
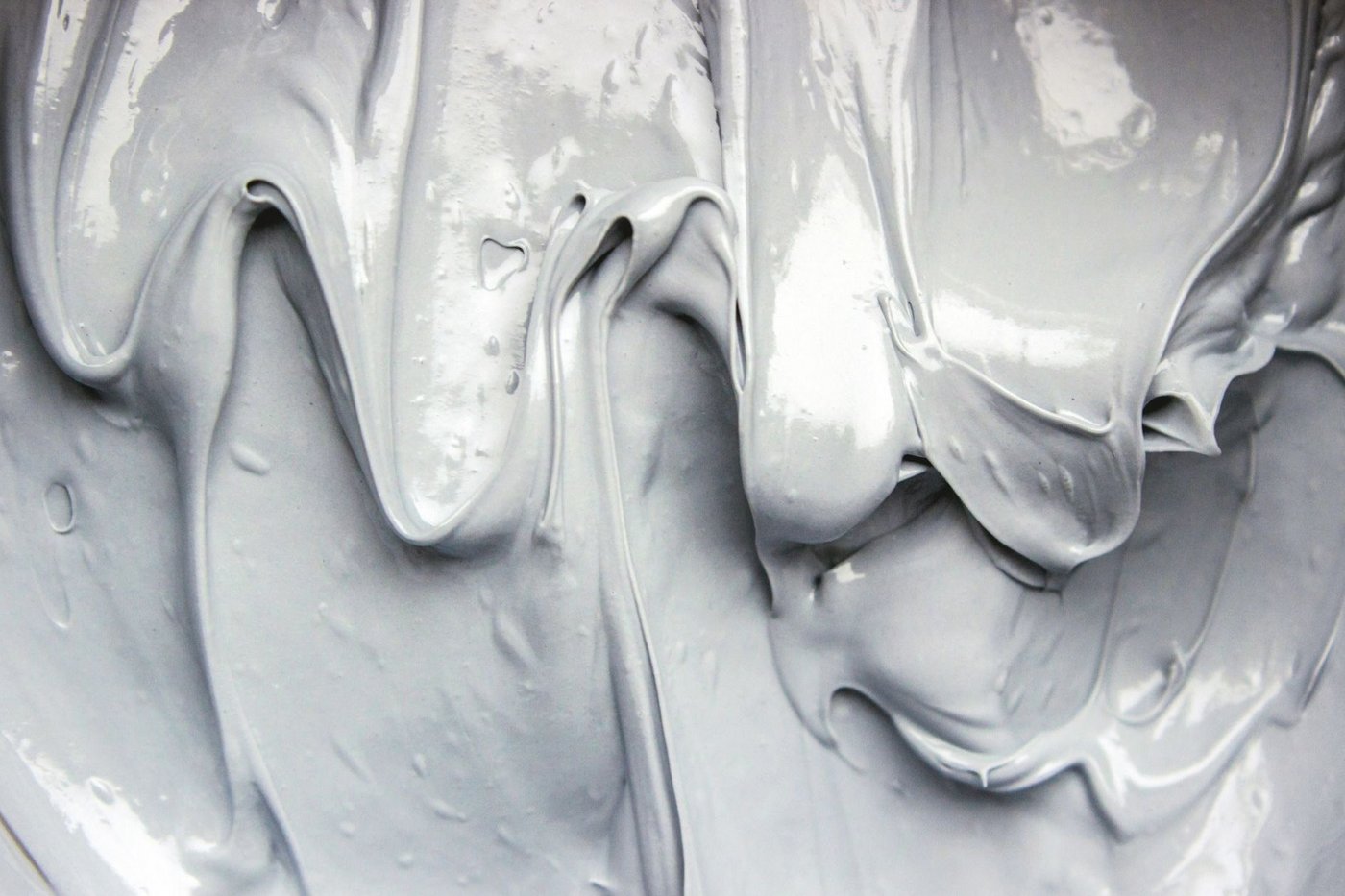
Media processed in the ceramic industry

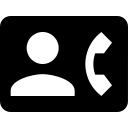
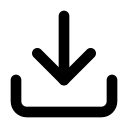
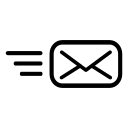