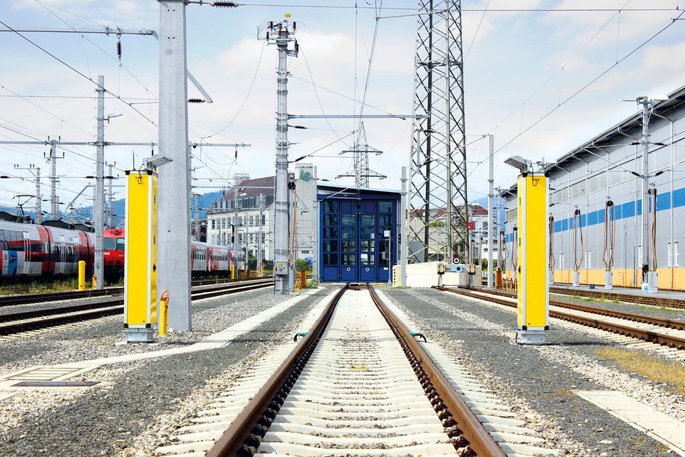
Identification for railway applications
UICScan
- Ready for immediate use, vehicles require no extra equipment
- Reliable thanks to use of video technology
- For high drive-through speeds
- Documentation of additional parameters, such as speed
- Can be combined with additional service systems
Scan and analyze rail vehicles in train station and maintenance areas
How the recording and evaluation of data with UICScan works
You’d like to know where your passenger train cars are currently located? Need an overview of vehicles in service and maintenance stations, or in washing bays? UICScan offers you a reliable and cost-effective option that can be used immediately without any additional preparation of the vehicles.
A specific UIC number is located at the center of each passenger train car. UICScan is capable of detecting these car numbers using an optical system. This uniquely identifies the car driving past and pinpoints its location. UICScan works with a special dual camera for day operations and – since it is equipped with special lighting – it is also reliable for night operation. The system records the numbers on both sides of the vehicle as it drives past.
UICScan can easily be integrated into train station or depot operations. It’s not necessary for the train to reduce its speed in the train station or depot. UICScan reliably records the vehicle number at pass-through speeds of up to 80 km/h.
The UICScan system also includes an axle counter. This combination can also document the speed as well as the vehicle number. UICScan can additionally be connected to the VEBSys train information system from Vogelsang. VEBSys enables online, real-time representation of the vehicles in question.
Typical areas where it is used include train entry and exit points at train stations, as well as service and maintenance stations or washing bays in which third-party cars are concerned and for which the costs must be calculated individually.
To install UICScan, no changes need to be made to the vehicle fleet. A 230V supply with 10A must be provided on-site at locations where the UICScan Tower is to be installed. Sun glare protection in the area where the images are recorded, as well as connection options to additional service equipment whose use is to be documented are also to be taken into consideration.
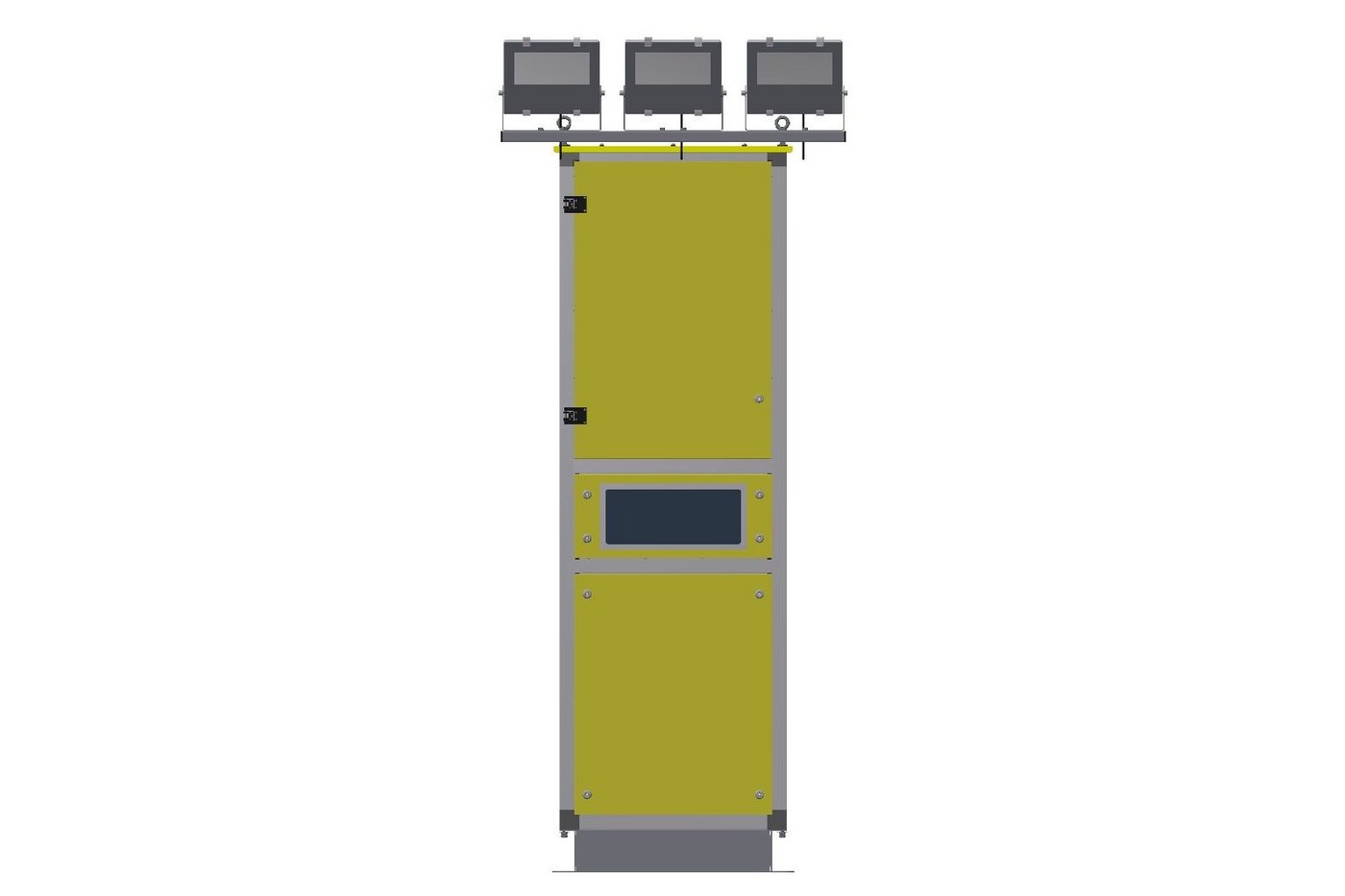
Models of the UICScan
UICScan consists of two units with
- UICScan Tower housing, incl. preparations for integration of QR code scanner
- Computer unit for speed interpretation purposes
- RC44 module (remote control)
- Dual-trigger module unit
- 24V-DC 10A power supply
- Software module to detect the UIC car number
- Software module for triggering
- Software module for axle counter with speed determination for each axle
- Online UMTS/HSDPA router
- Interface to train washing bay
- Axle counting with trigger module on the track
- Special dual camera (day/night mode)
- 3 power LED projectors
- 250W frost protection heating
- Concrete installation frame
- Optional: QR code long-range scanner
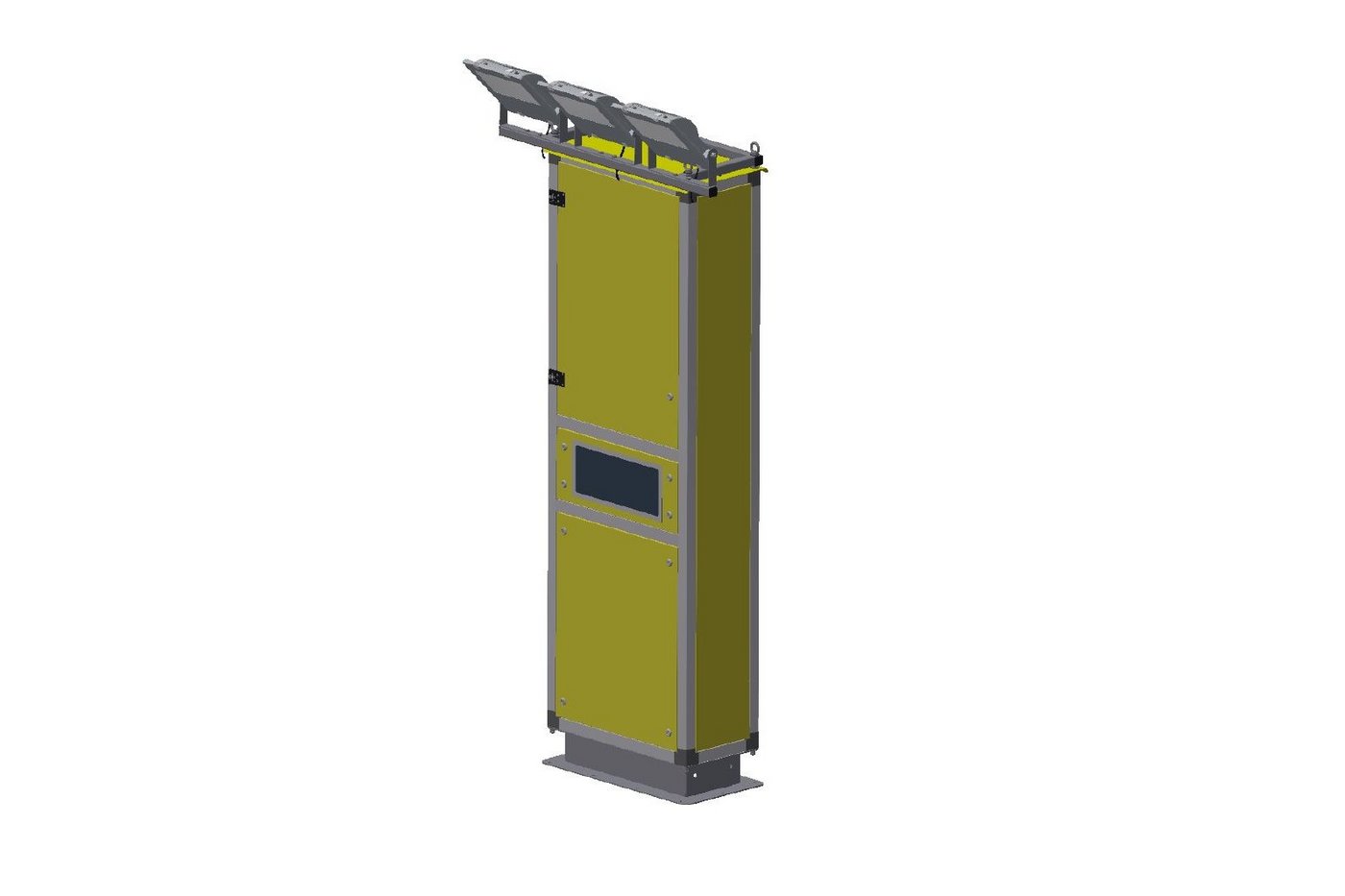
Recorded parameters
- Vehicle number (UIC car number)
- Optional: QR code interface 3
- Customer EVU
- Archive documentation
- Date and time
- Exterior temperature
- Drive-through speed
- Disruptions
- Video stream for subsequent processing
Downloads
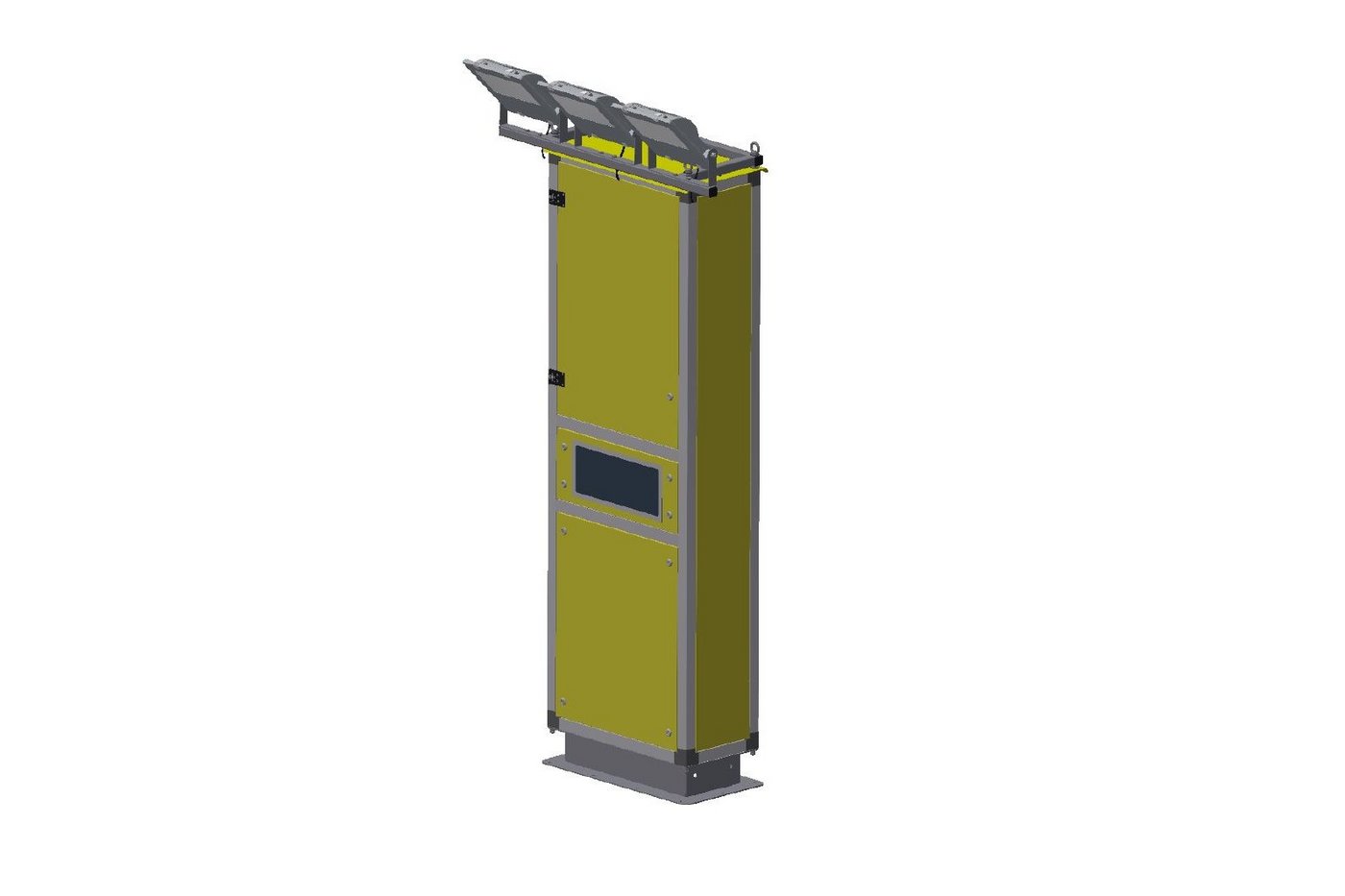
UICScan consists of two units with
- UICScan Tower housing, incl. preparations for integration of QR code scanner
- Computer unit for speed interpretation purposes
- RC44 module (remote control)
- Dual-trigger module unit
- 24V-DC 10A power supply
- Software module to detect the UIC car number
- Software module for triggering
- Software module for axle counter with speed determination for each axle
- Online UMTS/HSDPA router
- Interface to train washing bay
- Axle counting with trigger module on the track
- Special dual camera (day/night mode)
- 3 power LED projectors
- 250W frost protection heating
- Concrete installation frame
- Optional: QR code long-range scanner
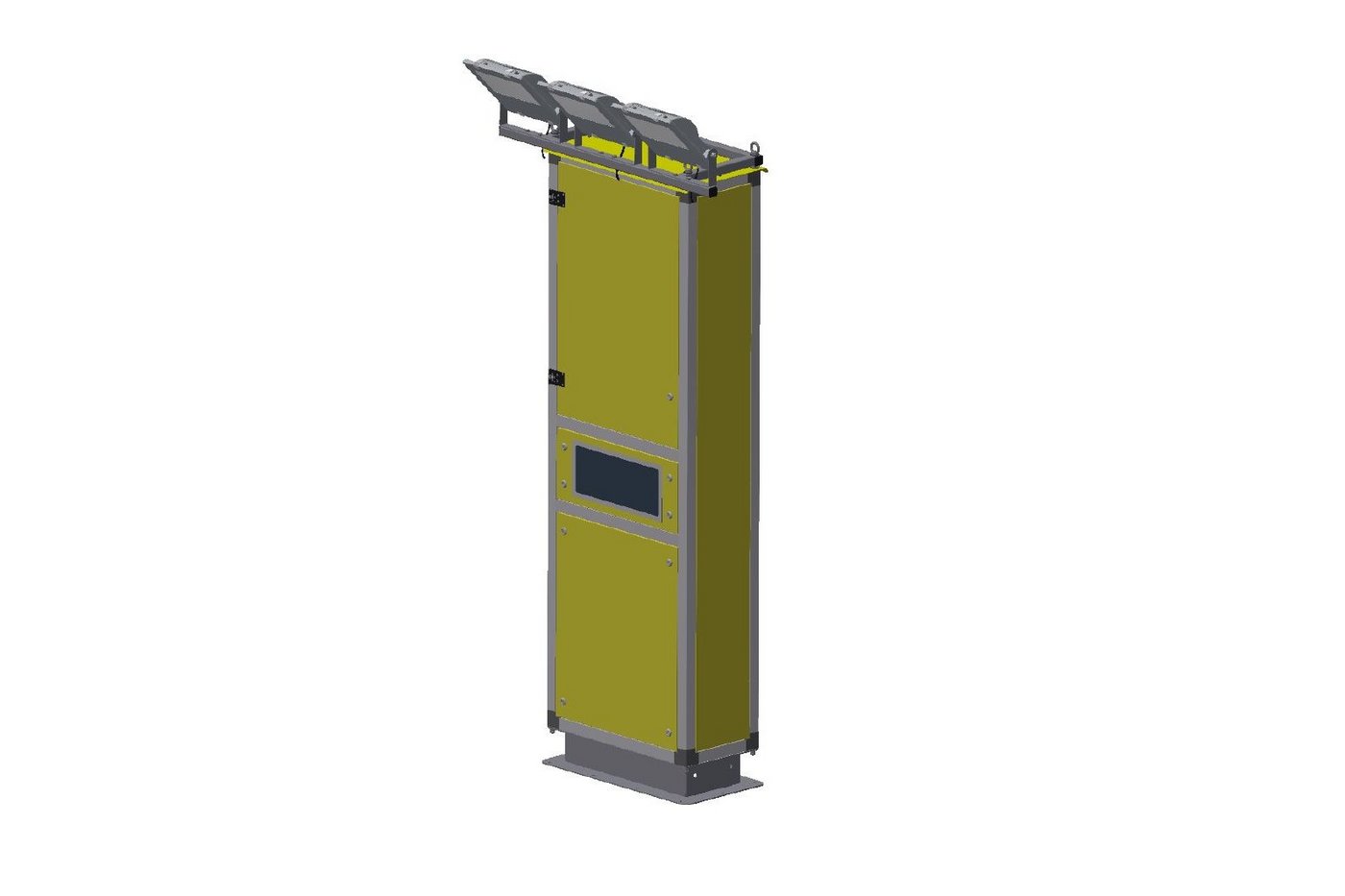
Recorded parameters
- Vehicle number (UIC car number)
- Optional: QR code interface 3
- Customer EVU
- Archive documentation
- Date and time
- Exterior temperature
- Drive-through speed
- Disruptions
- Video stream for subsequent processing
Downloads
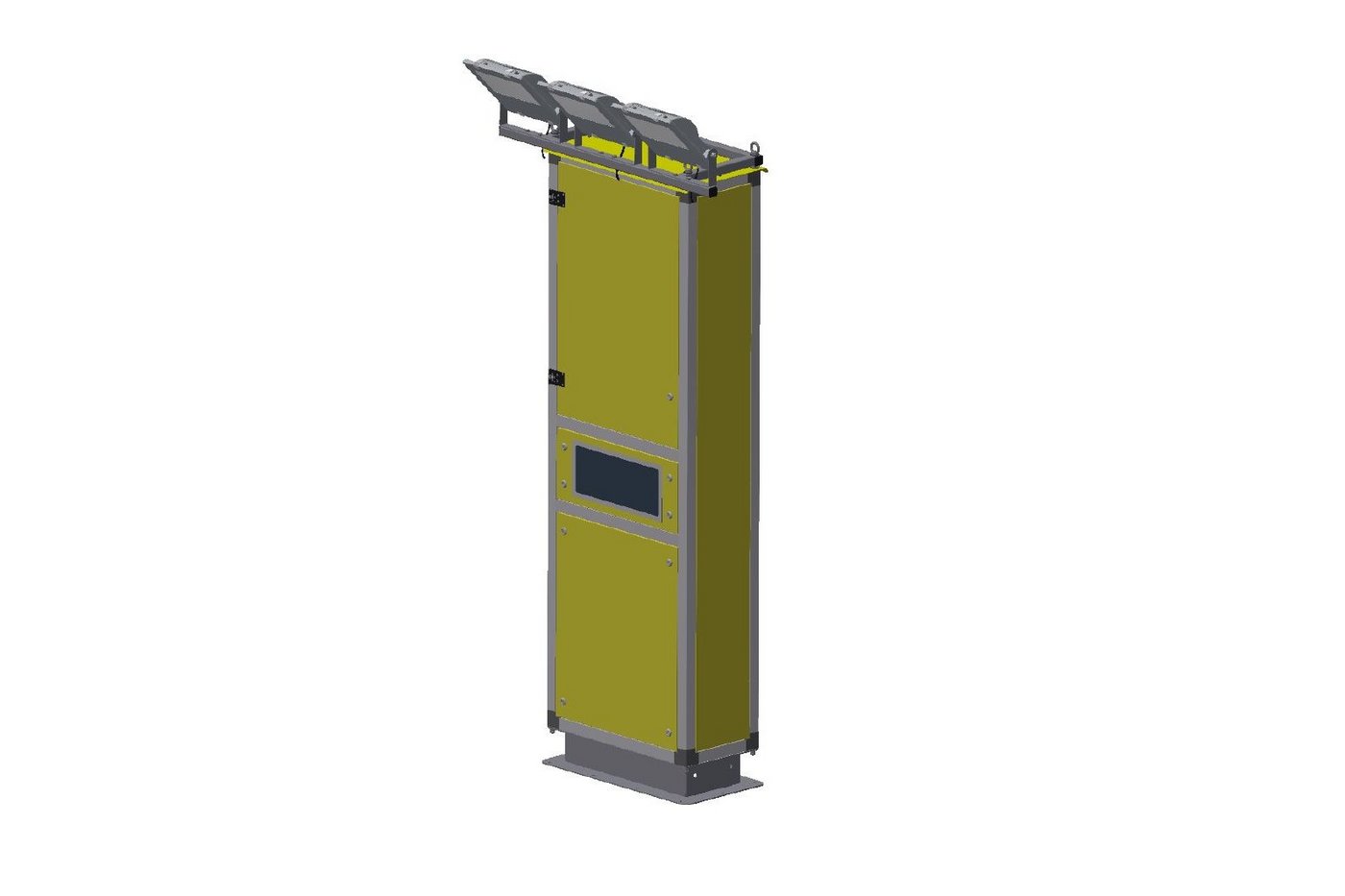
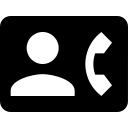
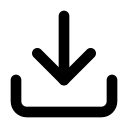
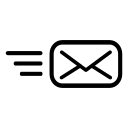